
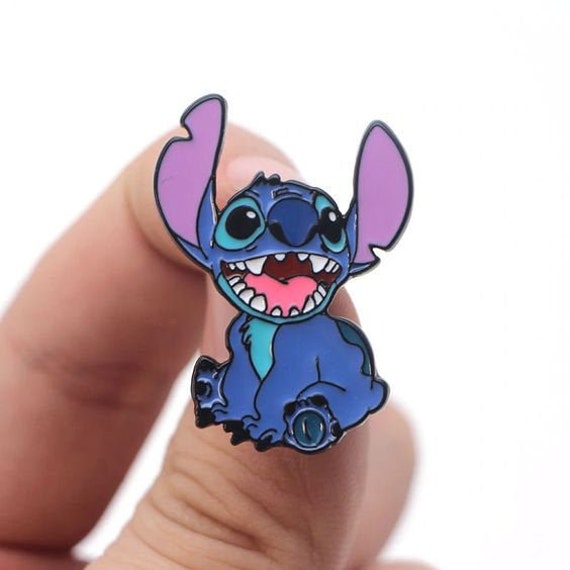
The above specification notes are for general guidance only and Helifix reserves the right to amend details/notes as necessary. In all instances the slot must be thoroughly damp or primed prior to injection of the HeliBond grout. Do not use HeliBond when the air temperature is +4☌ and falling or apply over ice. Ideally additional wetting of the slot, or priming with HeliPrimer WB, should be carried out just prior to injecting the HeliBond grout. In hot conditions ensure the masonry is well wetted or primed to prevent premature drying of the HeliBond due to rapid de-watering.
Castmaster stitching pins crack#
Where a crack is less than 500mm from the end of a wall or an opening the HeliBar is to be continued for at least 100mm around the corner and bonded into the adjoining wall or bent back and fixed into the reveal, avoiding any DPC. Normal vertical spacing is 450mm (6 brick courses). HeliBar to be long enough to extend a minimum of 500mm either side of the crack or 500mm beyond the outer cracks if two or more adjacent cracks are being stitched using one rod. For thin mortar joint specifications refer to the Helifix Technical Dept.
Castmaster stitching pins full#
Height of slot to be equal to full mortar joint height, with a minimum of 8mm. Depth of slot into the masonry to be 25mm to 40mm. An insurance-backed warranty via our Approved Installers scheme METHOD STATEMENT RECOMMENDED TOOLING GENERAL NOTES Specification Notes The following criteria are to be used unless specified otherwise: A.Devising and preparing complete repair proposals for specific situations.


Standard finger trowel If your application differs from this repair detail or you require specific advice on your particular project, call the Helifix Technical Sales Team on 020 8735 5222. Helifix Pointing Gun CS with mortar nozzle For smoothing pointing. 3-jaw-chuck drill with mixing paddle For injection of HeliBond into slots. Twin-bladed cutter with vacuum attachment For mixing HeliBond. Pointing may be carried out as soon as is convenient after the HeliBond has started to gel. Point up the remaining slot with a suitable matching mortar and make good the crack using an appropriate Helifix bonding agent depending on the width of the crack. Inject additional HeliBond as necessary, leaving 10-15mm for new pointing.
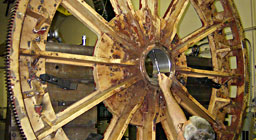
Inject a second bead of HeliBond grout over the exposed HeliBar and iron it into the slot using a finger trowel. Push the 6mm HeliBar into the grout to obtain good coverage. Mix HeliBond cementitious grout using a power mixer and load into the Helifix Pointing Gun CS. Ensure the slot is damp or primed prior to commencing step 5. Where the substrate is very porous or flushing with water is inappropriate, use HeliPrimer WB. Remove ALL dust and mortar from the slots and thoroughly flush with water. Ensure that NO mortar is left attached to the exposed brick surfaces in order to provide a good masonry/grout bond. Using a twin-bladed, diamond-tipped wall chaser and vacuum attachment, cut slots into the horizontal mortar joints, to the specified depth and at the required vertical spacing. Peen each 1 inch weld with this method too.HELIFIX MASONRY REPAIR DETAILS © April 2009 Crack Stitching a Cavity Wall using HeliBars CS01 1. Never allow the metal to get so hot that you can't place your hand on it. Once a good weld deposit is made, the two sides of the crack can be welded together. Using the methods discussed above, weld the studs in place and cover the entire surface of the break with weld deposit. This type of pin can actually hold a crack together rather than just fill it, and may be used to repair cracks that cant be fixed with ordinary tapered or straight pins. "Castmaster" pins (manufactured by Lock-N-Stitch) have a unique "spiral hook" or "reverse pitch" thread pattern that grips both sides of a crack when the top shoulder of the pin bottoms against the metal. Screw steel studs into the threaded holes, leaving 3/16 to ¼ of the stud above the surface. After welding allow the block to cool slowly be insulating it.Īnother choice is to not preheat it at all.ĭrill and tap holes over the surfaces that have been beveled to receive the repair weld metal. V- groove the crack and Weld in 1 inch long segments and peen the weld after each bead. Aim for 1200 degrees.īut never, I repeat never over 1400 degrees since its effects the characteristics of cast iron at that temp. Hard to preheat a block being its so damn big and acts like a heatsink constantly sucking the heat away from the effected area.Įither preheat between.500-1200 degrees. Never heard of using stainless on cast iron although I'm not saying its not a choice.
